It is important to get the building envelope right the first time. It’s almost impossible to repair a problem once you cover it up with siding or shielding. By ignoring this important aspect of building, you are creating a path towards a leaky house, which could lead to poor air quality, moisture deposits on cold surfaces, and mildew.
The problem with a poor building envelope
Leakage from exterior building enclosures can affect our health. Air barrier gaps and cracks can lead to a number of problems. These gaps allow bugs, dust and pollen in, but they also let cold or warm air, moisture, and contaminants into the home. This leakage may have negative effects depending on where you live.
In humid climates, excessive leakage of the building envelope can lead to excess moisture infiltrating your home. This makes it uncomfortable and susceptible to indoor air quality (IAQ) problems, such as mildew.
In drier climates the opposite occurs. Dry air can enter the home during winter and create an uncomfortable, dry environment. This can lead to dry sinuses and static electricity and may even spread viruses. Leaks can also increase energy consumption, since the heated or cooled air leaves the building faster, resulting in longer air conditioner and heater runs.
And that is why a blower door test is so critical to your process, whether you are building residential, multifamily, commercial, new construction or restoration/retrofits. Since the beginning of the industry, professionals have been aware that better duct seals, enclosure seals, and improved air quality are needed. The blower door test will determine if the problem has occurred on a particular project.
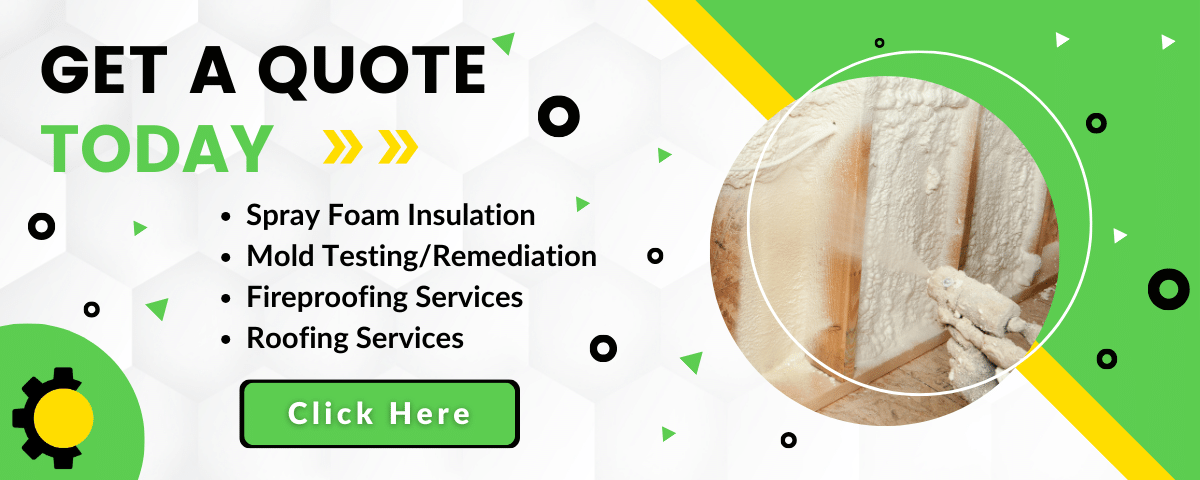
What is a blower door test?
Blower door tests are used to measure the air leakage in buildings. In this test, the fan is calibrated and installed in a sealed window or door. All other exterior openings are also closed. The fan creates a difference in pressure between the outside air and the interior when it is on. The fan, which is usually operated under negative pressures, suctions air from the house, forcing it into the home through any and all possible pathways.
Professionals measure these unintentional leaks when they perform these tests. The air that is going through the fan, while the pressure is constant inside the building, is the total of all leaks. The fan’s airflow is known at different pressures because it is calibrated. We can know the air volume that will leak through cracks and gaps if we maintain the pressure differential. It’s like adding water to an overflowing bucket. You can measure the amount of water leaking out if you keep the bucket level constant and know how much water you are adding.
These tests separate the indoor area from the outdoor space and measure the leakage. You can’t improve something you don’t measure. But enclosure testing is not just about getting a number. After locating the source of leakage, you can make recommendations to fix it. Air coming through an open window is different from air entering through an attic with fiberglass insulation that has been poorly sealed. Air flowing through a leaky window won’t pick up pollutants, or cause materials to get wet like an attic air leak might.
People who are concerned about their health, comfort or efficiency should test their homes to find out how they measure and what can be done to improve them. Blower door testing is relatively new in the United States. Many builders have blower door testing done for their builds. However, fewer stay and observe the process. Watching the process for builders can improve their next build.
Blower door tests are also recommended to ensure that your air conditioner or furnace is sized correctly. Imagine that you own a boat with some holes. The boat starts to sink. What size bilge pumps do you need to prevent water from entering the boat and sinking it? This would depend on the number of leaks in your boat. How leaky or tight your home is can change how much heating/humidification or cooling/dehumidification you need. The design of your mechanical system will be affected by this. Ask your designer if and how air leakage metrics are used in their load calculation.
Measurement of leakage
The envelope leakage is calculated in terms of volume of air per time unit. In the U.S. we use CFM, or cubic feet of air per second. We then convert that number into a standard metric known as ACH50, which is the air changes per hour for a test pressure of 50 pascals. The ACH50 metric indicates the number of times the air volume inside a building changes in comparison to the outside air when tested. This translates into air leakage during normal conditions. The ACH50 is the most common way to compare air leakage between homes. However, there are also other methods, such as CFM/sqft of floor space and CFM/sqft of building envelope.
When and how to have a blower-door test
The blower door test is usually done at the end of construction of a home. This is when the final paint has been applied, the doors and windows have been installed, and the weatherstripping is in place.
It is the perfect time to get your final numbers. However, as we have already mentioned, it’s not the best time to fix any problems that may arise. Leakage testing can be done at various stages of construction to diagnose problems and fix them, while the primary air barrier remains accessible. This early testing comes with a caveat: you need to seal any windows or doors that have not been filled in yet. Otherwise, you will not be able to pressurize the structure enough to find leaks.
It is possible and recommended that builders purchase their own testing equipment. However, it will be a significant investment. Builders can save money in the long term, especially if their code tests are failing. It can be used as a tool for subcontractors to ensure that they have completed the job correctly. You can also gain valuable knowledge by testing things yourself.
Achieving energy-efficient building envelopes
Air-sealing a home can help you save energy depending on several factors, including the climate zone in which you live, how much heat or cold you maintain inside your home, and the amount of wind that your home may experience. In 2009, the International Energy Conservation Code required a building envelope leakage level of 7 ACH50. Now in 2018, code requires 3 to 5 ACH50 across most of the United States. The trend of decreasing leakage requirements shows that building codes are likely to continue getting more strict over time, as builders become accustomed to the new standards and as technologies and products improve. It is possible to achieve an ACH50 between 3-5. Passive Houses are now required to meet a 0.6 ACH50. This is all done to reduce energy consumption on a massive scale.
Sealants are available on the market to ensure that your building envelope is tightly sealed. But they’re all not created equal. PROSOCO fluid-applied sealants, for example, are independently tested and code recognized. They also have a long track record of success compared to other products. R-Guard fluid applied silyl-terminated Polymer (STPE), a product of the company, creates a monolithic layer that is impermeable but permeable enough to allow buildings to breathe. This combination ensures that performance is maintained even when buildings move and climate conditions change. Because they are applied fluidly, products like PROSOCO’s FastFlash or AirDam make sealing and flashing around windows and door frames (where most leaks occur) easier than the traditional sheet-type methods. This system installs windows and doors that ensure blower door tests are successful faster.
If you think your home needs a home energy audit, call us today!